Rolled Thread Type Features
Precision-rolled for precision and low price
The screw shaft is formed using a precision thread rolling process, delivering higher surface precision at a lower price compared to conventional cutting processes.
Tolerance is 7H for nuts, 7e for shafts.
Production/inventory systems ensure availability at short notice
Large-scale production allows delivery of trapezoidal rolled threads at short notice and at low price.
Nuts and screw shafts are always held in stock for immediate delivery.
Materials
Shafts:S45C, or SUS303
Nuts:BC-6
Part number composition
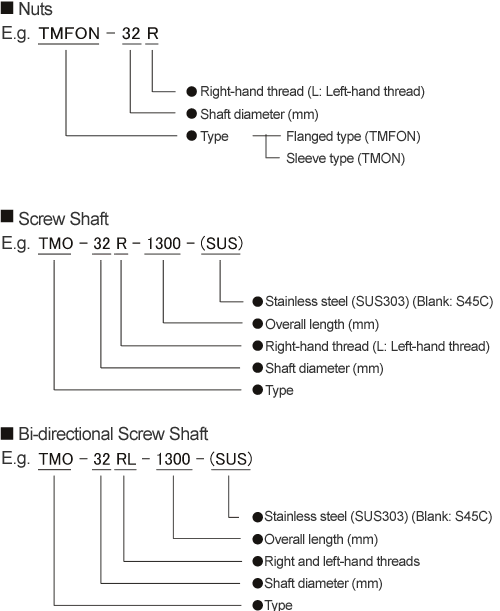
Cut Thread Type Features
TMF-series feed screws are based on the commonly-used JIS B0216 metric trapezoidal screw thread.
Many commercially-available trapezoidal feed screws are formed by heavy cutting. This can result in several problems such as large cumulative lead error, and quick abrasion due to roughness of the face where nut meets shaft core or threading surface roughness. Often such feed screws will not work as required.
ASK has therefore leveraged its precision processing technology to create the TMF series of precision feed screws. The nut is made of cast bronze (BC-6), improving resistance to wear and lowering the coefficient of friction, thereby enabling long-term usage. Lapping can also be applied on request. RoHS-compliant nuts are also available.
Precision
Single pitch error | Cumulative pitch error | |
Nut | — | ±0.01 (over total nut length) |
Shaft | ±0.015 | 0.05 (over 300mm) |
Materials
Nuts:Cast bronze (BC-6) (RoHS-compliant nuts also available)
Shafts:Steel for mechanical structures (S45C)
Available threading lengths
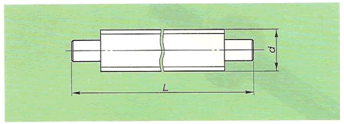
d | L / d |
---|---|
10-14 | 30 |
16-25 | 40 |
28-50 | 50 |
Part number composition
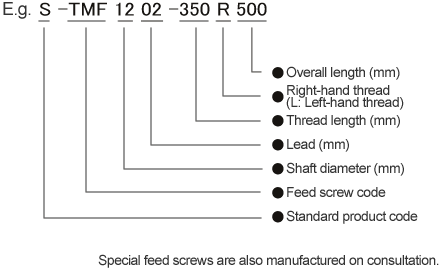
Precision Thread Type Features
Precision
TMFG-series made-to-order feed screws consist of commercially-available metric (M) and trapezoidal metric (TM) screws to which hardening and cutting are applied.
The table below shows precisions for the TMFG series.
- Axial clearance (mm)
Precision code | 05 | 10 | 20 | 30 | 50 |
---|---|---|---|---|---|
Axial clearance | Up to 0.005 | Up to 0.01 | Up to 0.02 | Up to 0.03 | Up to 0.05 |
It is possible to keep axial clearance to 0.01mm through nut design.
- Thread precision and axial clearance combinations
Grade | Precision code | ||||
---|---|---|---|---|---|
05 | 10 | 20 | 30 | 50 | |
C1 | C1-05 | C1-10 | ― | ― | ― |
C3 | C3-05 | C3-10 | C3-20 | C3-30 | ― |
C5 | ― | ― | C5-20 | C5-30 | C5-50 |
Materials
Custom orders using other materials are also accepted.
Shafts: SK-3, SCM415H, SUS440C, SUS304, etc.
Nuts: BC-3, BSBM2, resin, etc.
Available threading lengths
Maximum screw shaft length for each precision grade (mm)
Shaft diameter | Precision code | ||
---|---|---|---|
C1 | C3 | C5 | |
6 | 120 | 180 | 200 |
8 | 160 | 240 | 280 |
10 | 200 | 300 | 350 |
12 | 240 | 360 | 420 |
14 | 280 | 420 | 500 |
15 | 300 | 450 | 530 |
16 | 320 | 480 | 570 |
18 | 360 | 540 | 640 |
20 | 400 | 700 | 1,000 |
It is possible to keep axial clearance to 0.01mm through nut design.
Part number composition
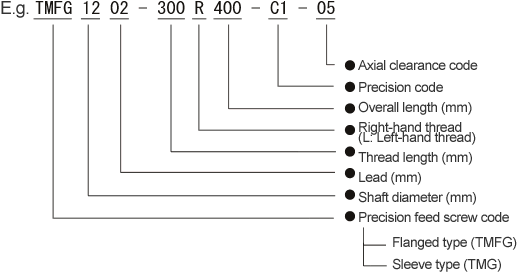
Nut selection
- Dynamic permissible torque (T) and dynamic permissible thrust (F)
Dynamic permissible torque (T) and dynamic permissible thrust (F) indicate the torque and thrust at which contact pressure on the tooth surface of the bearing is 1kgf/㎟. These values are used to gauge the strength of the nut.
- pv value
The pv value – the product of contact surface pressure (p) multiplied by sliding speed (v) – is used to determine whether a sliding bearing can be used. Please refer to pv values in the graph below when selecting TMF-series nuts. Lubrication conditions also affect the pv value.
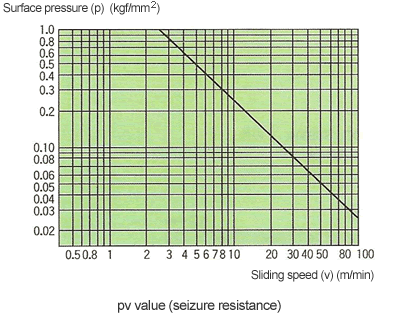
- Calculating contact surface pressure (p)
Contact surface pressure (p) is reached using the following formula.

- Calculating sliding speed (v) over teeth
Sliding speed (v) is reached using the following formula.
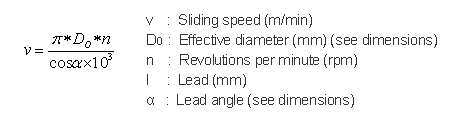
- Safety factor (fs)
When calculating the load to be applied to a nut, it is necessary to accurately determine the effect of inertia forces, which change with the weight and speed of an object. With machines that rotate or move back and forward, it is generally difficult to accurately determine all factors such as the impact of constant starting and stopping. If the actual load cannot be ascertained, the table below must be used for bearing selection.
Safety factors (fs)
Type of load | Lower limit of fs |
tatic load, low usage frequency | 1-2 |
Standard one-way load | 2-3 |
Load affected by vibrations/impacts | 4 or above |
- Temperature factor (fT)
Because a nut’s seizure resistance and the strength of its material deteriorate if temperature rises above normal temperature, it is necessary to multiply the dynamic permissible torque (T) and dynamic permissible thrust (F) by the corresponding temperature factor in the table below.
Temperature factor (fT)
Usage temp. | Up to -20°C | -20°C-5°C | 5°C-60°C | 60°C-120°C |
Temp. factor | 0.2 | 0.2-0.5 | 1.0 | 0.5-1.0 |
Accordingly, the selected nut must satisfy the following equations relating to strength.
Dynamic permissible torque (T)

Dynamic permissible thrust (F)

- Calculation example for nut selection
Select a nut for a TMF-type feed screw. The nut must travel at a feeding speed (S) of 2m/min bearing an axial load (PF) of 100kgf applied in one direction.
- pv value
Provisionally select TMF28-5. (Dynamic permissible thrust (F) = 1,830kgf)
Determine contact surface pressure (P).

Ascertain sliding speed (v).
Determine shaft revolutions per minute (n) required for a feeding speed (S) of 2m/min.

From the pv value graph, it is determined that no major abrasion will occur if sliding speed (v) is 44m/min or below for a contact pressure (p) value of 0.055 kgf/㎟
- Safety factor
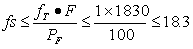
From usage conditions, temperature factor (fT) = 1, load = 100kgf.
If the safety factor is 2 or above, strength is adequate. TMF28 is selected.
Efficiency and thrust
フィードスクリュウでトルクを推力に変える効率(η)は、次元で計算されます。

The efficiency (η) with which a feed screw converts torque into thrust is calculated using the following.

- Calculation example
Assume we are calculating the thrust generated when using TMF20 (with torque (T) = 1.5kgf•m).
Calculate efficiency (η) when μ = 0.15.
TMF20 lead angle (α) = 4°03’.
According to the graph below, when μ = 0.15, efficiency (η) = 0.315.
Calculate thrust generated (Fa).
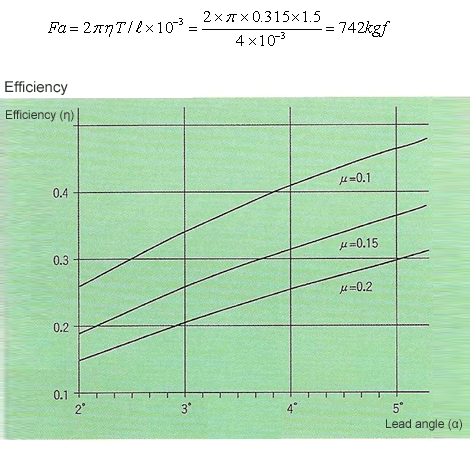
Lubrication
The speed, load and temperature at which a feed screw operates are factors to consider when selecting a lubricant. As a general rule, use low-viscosity oil or grease with a low consistency number for high speeds and loads.
When using a centralized lubrication system for grease application, grease with good fluidity during lubrication should be selected. Take special care during lubrication to prevent foreign substances mixing with the grease.